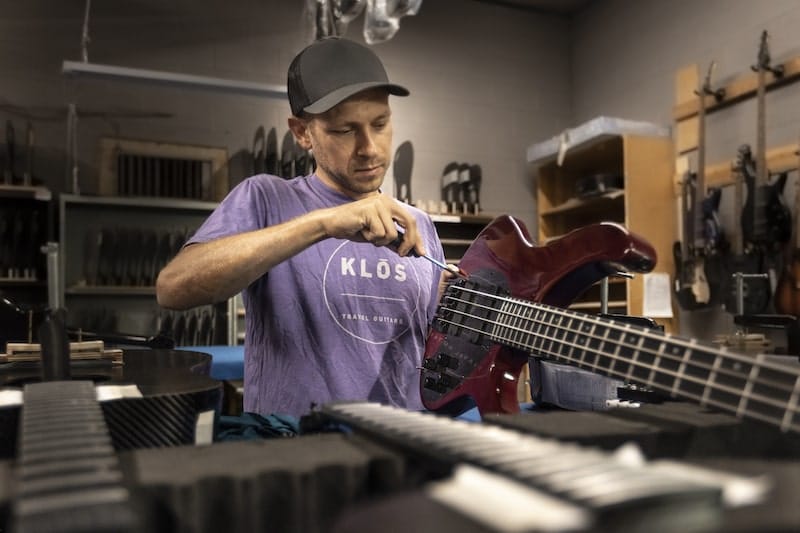
KLOS Guitars, Utah’s only large-scale guitar manufacturing facility, is internationally distributed, but reflects the rugged adventure found from the mountains to the deserts of our Utah landscape.
For those who want to marry the adventure to the art within themselves, there are really two instruments that stand out as mascots for life out in the world ― the guitar and the ukulele. If you pull out a ukulele around a campfire and start singing Smash Mouth’s All Star, you’re likely to get a round of off-key social bonding.
If you’re couch surfing across the nation and you pull out a guitar in the apartment of some new friends, someone will want to show you their rendition of Wonderwall or Stairway to Heaven. These sorts of memories are branded into our minds, and stories are banked for later withdrawal in our sunset years.
If a traveler has an instrument, it is likely to be a guitar or ukulele, but it’s also likely to be in rough shape as a consequence of the traveling lifestyle. Even if you can afford to travel first class on an airplane, the baggage handlers probably don’t hold the same reverence for your instrument that you do.
The folks at KLOS aren’t just making another guitar. They are making a guitar that can tag along with the world explorer. Ian Klosowiak who, along with his brother Adam Klosowiak, founded KLOS, put it this way: “We wanted our guitars to be a piece of gear. Your wood guitar is a piece of art that you want to protect. We want you to throw our guitar in the trunk with your other adventure gear and not worry if it can handle the trip.”
Ian is soft spoken, but you can tell he knows the lifestyle his guitars are meant for firsthand. His experience with adventure has clearly been drawn upon when designing the patented features of the guitar, but it also spawned another local Utah business from the two brothers: www.skillboardusa.com. Skill Board is a core strengthening balance board for extreme sport training.
In the promotional videos for their guitars and ukuleles, the brothers drop cinder blocks on their instruments and drive over them with a car. What makes them so durable is carbon fiber construction. Ian noticed that the mountain biking world had embraced carbon fiber years ago, but the only guitars utilizing the strong, lightweight material were $3,000 plus. That wouldn’t do. They needed to be more affordable. Klos guitars range in price from a little over $600 to around $1500.
Ian went to BYU for mechanical engineering, and he built his first carbon fiber guitar there. This set fate into motion. When he took it with him to travel around Europe, he got a lot of compliments on his workmanship. For a student looking forward to the next phase of his life, where he would soon need to carve his own space out of the business landscape, this experience and feedback were inspiring.
Could he sell a recipe that was one part guitar hobby, one part adventure traveler, and two parts engineer? He knew he could make a professional level instrument that was very light, which helps when traveling, and he didn’t have to sacrifice sound quality for weight and strength. A big reason there isn’t a compromise is that the strength of the material itself meant the soundboard (the top of the guitar body) could be thin and didn’t need to be supported with the X bracing used in wooden guitars, freeing up the material to resonate better.
Back at BYU, Ian entered into a business competition in which he did well. When his brother Adam came to visit on a ski trip, they decided to enter a similar competition at Princeton University where Adam was studying electrical engineering. They won $20,000 which they used as seed money to start Klos guitars. They opened up shop in Provo, Utah, and Ian and Adam now have twenty employees building guitars for them.
They choose their staff by finding musicians who know what they want in their own guitars, and then educate them in the industrial arts required to fabricate tools of creativity that they would want to play themselves. Ian tells me this approach has “produced great results”, and players all over the world would agree with him.
Subscribe to Utah Stories weekly newsletter and get our stories directly to your inbox